Military 3D-printing face shields, reusable N95 masks to address hospital shortages
The efforts will increase critical equipment as hospitals combat the coronavirus
The U.S. military is 3D-printing face shields, designing reusable plastic N95 masks and sewing surgical masks to increase the supply of critical medical equipment as hospitals across the U.S. work to combat the coronavirus pandemic.
Nine Navy and Marine Corps commands began their 3D-printing efforts on March 28 after the Federal Emergency Management Agency requested the initial production of 220 medical face shields, the Navy said in a news release.
Days later, the assistant secretary of the Navy for research, development and acquisition authorized all of its commands to support FEMA requests, saying that the country is in a national emergency so they "must engage accordingly."
The U.S. military is uniquely poised to assist in the production of personal protective equipment because of its expertise in additive manufacturing, or 3D printing.
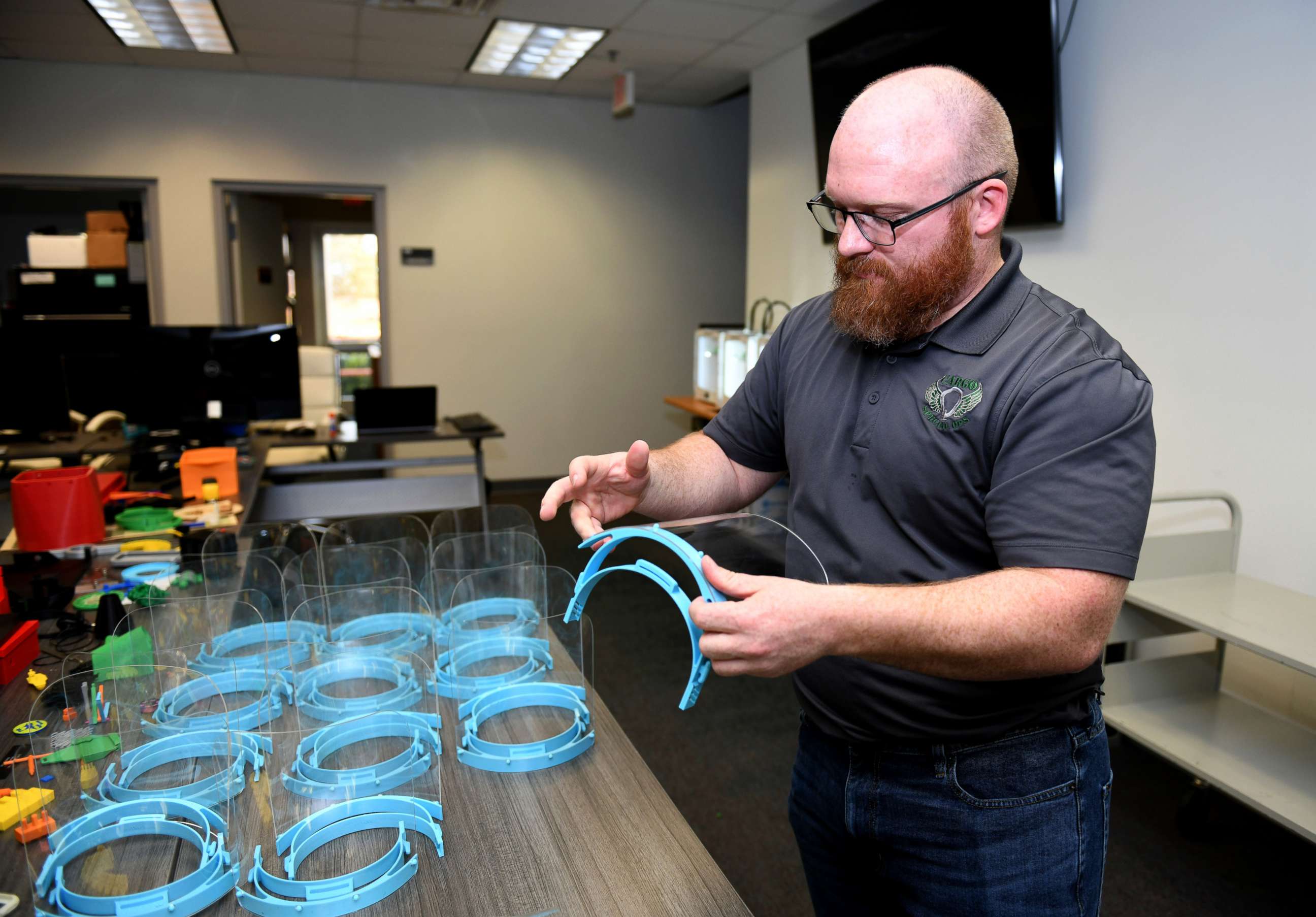
The Marine Corps' Advanced Manufacturing Operations Cell (AMOC) was the first to receive FEMA's request for 220 face shields before alerting other Department of the Navy manufacturers.
"Every (additive manufacturing) producer I reached out to stepped up," said Marine Capt. Matthew Audette, an advanced manufacturing project officer with AMOC. "It speaks volumes of our additive manufacturing community that every group was confident that they could produce the entire request on their own. We broke it up to distribute the load."
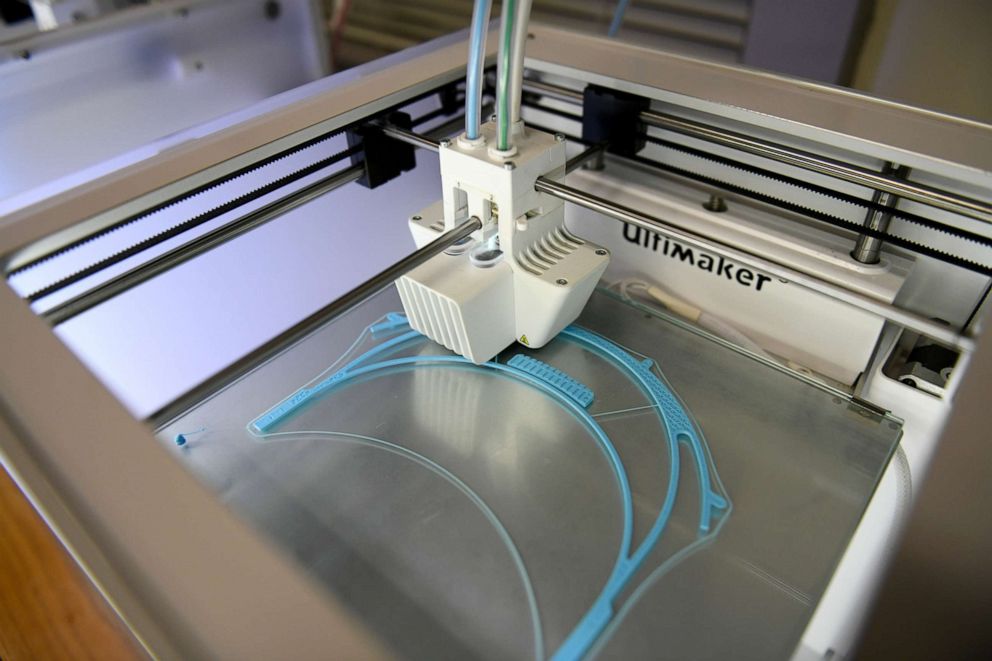
According to the Navy, the department is now working with the Pentagon and industry "to determine the volume and scope of (additive manufacturing) requests, the capacity to manufacture and distribute production across sites and ensure quality standards."
And those efforts are extending across the entire U.S. military.
Some Air Force instructors have started 3D printing, not only face shields, but reusable plastic N95 face masks, the service said.
Instructors with the 312th Training Squadron's Special Instruments Training course at Goodfellow Air Force Base in Texas were inspired by similar efforts they saw on social media.
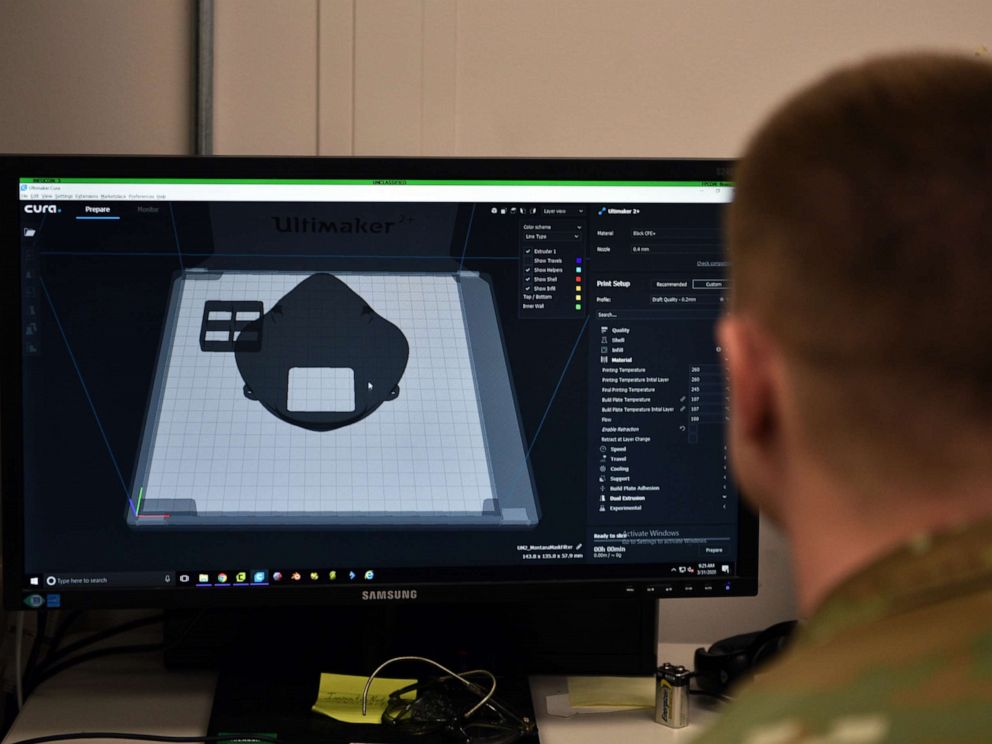
“We saw other people 3D printing medical supplies, and we thought we should try printing things like face masks and face shields,” said Master Sgt. Manuel Campo, special instruments training flight chief.
The instructors found a free model online for a 3D-printable, high-efficiency filtration mask designed by a neurosurgeon in Billings, Montana, who worked with a dental company to create the masks.
The group plans to present their prototypes to a medical group to see if they can meet hospitals' needs during the pandemic.
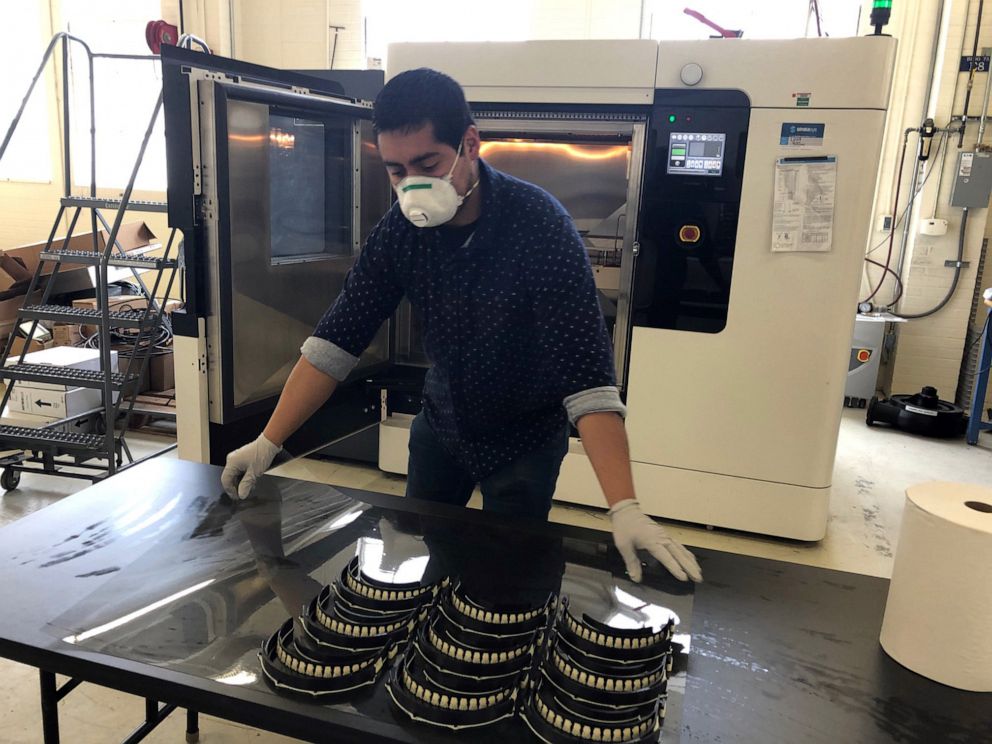
At Joint Base Lewis-McChord in Washington, 1st Special Forces Group soldiers who normally use sewing machines to repair parachutes are now producing surgical masks, according to the Defense Department.
The Group Support Battalion is creating the masks, along with prototypes for respirator masks and 3D face shields, for its local Madigan Army Medical Center and regional partners.
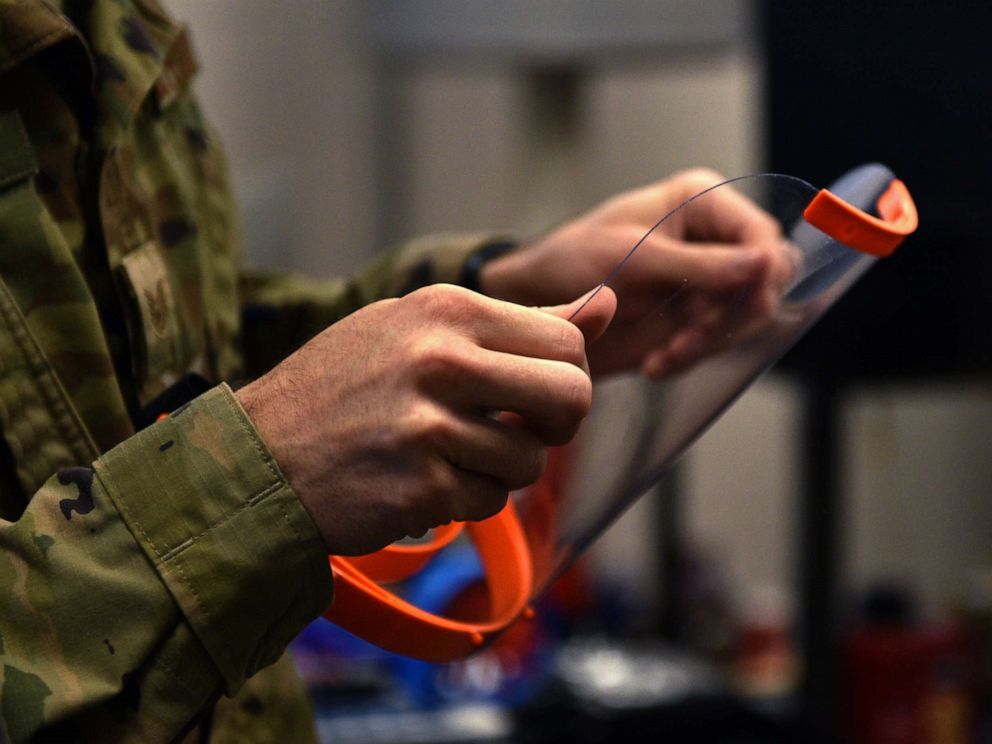
The Aerial Delivery Platoon is already able to produce 200 masks in a day with expectations to eventually produce 1,000 to 1,500 masks per week, said Army Lt. Col. Christopher S. Jones, the battalion's commander.
"I believe this is a phenomenal effort to help our health care professionals and fellow Americans," Jones said. "We're collaborating with (Army Special Operations Forces) and conventional forces across the Army to make a difference. The effort in and of itself is a worthwhile exercise in how to innovate to provide solutions, especially as the U.S. military has the best capability in the world."
What to know about coronavirus:
- How it started and how to protect yourself: coronavirus explained
- What to do if you have symptoms: coronavirus symptoms
- Tracking the spread in the US and Worldwide: coronavirus map