Supply chain problems forcing small businesses to change how they operate
Supply chain issues have taken a toll on small businesses importing materials.
The supply chain issues the U.S. economy is currently facing are not only affecting consumers during the peak shopping season, but small businesses have also started to feel the effects of these shortages.
According to the most recent U.S. Census Small Business Pulse Survey, conducted between Oct. 11 and Oct. 17, 45% of businesses said they are having domestic supplier delays. The number is up from 26.7% during the first week of the year.
Supplies that small businesses rely on are becoming harder to find, especially since owners cannot always order in bulk or in advance like larger companies.
Rene Kirby, the owner of Marie's Cafe in Baltimore, works to provide baked goods from her home and in pop-up shops in her community. With essential products not available on shelves, Kirby has been left searching for answers.
"We just can't serve the same size beverages, or sometimes any beverages, because they don't have the cups we need in stock," said Kirby, adding that buying these essential products from other suppliers increases the price, making it "difficult for the consumer to buy these products."
Jeremy Plemons, the owner of County Manners, a food truck based in southern Maryland, said he has been going to the same businesses for the past six years and has been shocked recently by the lack of products at his local stores. He said he has had trouble finding to-go boxes and forks, essential for his food truck business.
"It would be one thing if I couldn't find french fries, we can change that, but when we got nothing to put it in, it's heartbreaking and stressful," Plemons said.
Plemons said he is looking to his community of restaurant owners to find a short-term solution for the most essential items he needs.
"We have been supporting each other a lot. If anyone needs anything, they know to call me, and I can always call them," said Plemons, mentioning he might buy a shipping container with a fellow small business owner to stock up on essential, single-use items.
The Biden administration has worked on ways to mend issues with the supply chain, including expanding work hours to 24/7 at Los Angeles and Long Beach ports and agreeing with large private companies to expand their hours as well.
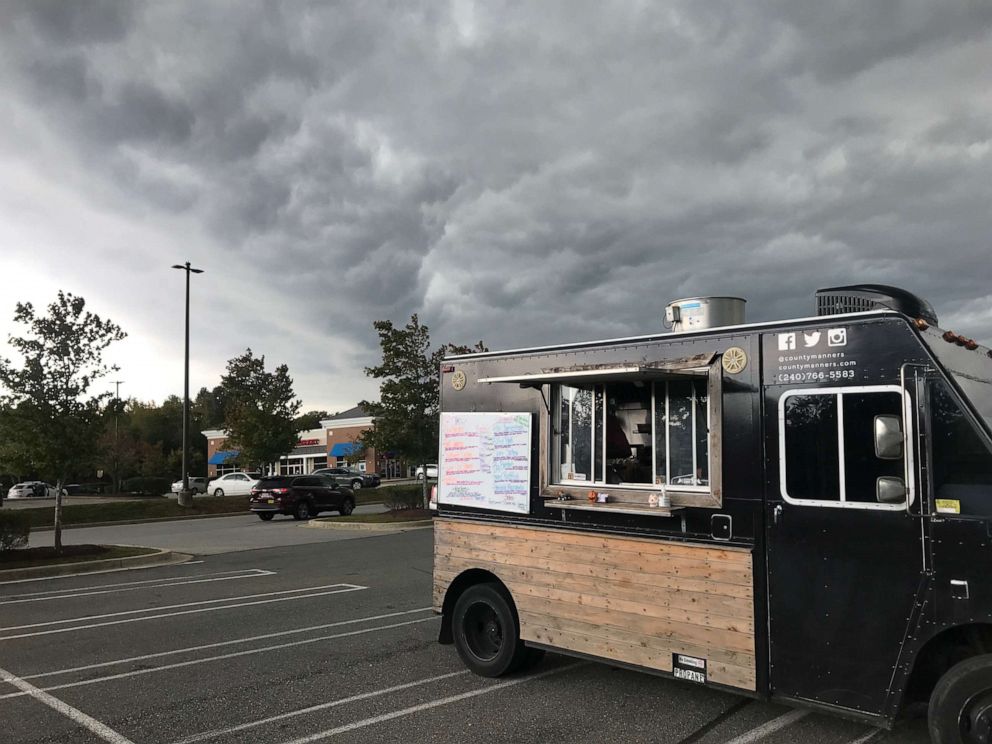
Easing the supply chain bottleneck is one step in the right direction, according to Ayman Omar, an associate professor of supply chain management at American University's Kogod School of Business.
Omar describes the current situation as a "perfect storm." Adding that "there is no one single point in time where the delays or disruptions started, it just exacerbated significantly because the volume of disruption is much higher," pointing to the disruptions in multiple fronts, including the current shortage of truck drivers, stocking up on products, and delays in the shipping industry.
"The worst thing for a supply chain manager is inconsistency, getting 10 units one day 100 units the other day, drives supply chain managers insane," adding that stocking up is also hurting small businesses "because a business is now ordering more of a product, another business might not get their product, it's just a big domino effect."
The outlook for small businesses is improving after many were forced to close during the COVID surge last winter. According to a survey conducted by Facebook and Small Business Roundtable, 16% of small to medium businesses in the U.S. remained close in July 2021, down from 22% in February. However, the speed of supply has not improved during the reopening phase of COVID, according to Omar.
"The infrastructure is at its breaking point, in terms of being able to deal with demand and distribution of supply," said Omar. "The massive amount of demand that has shot up over the last five to 10 years, capacity has not kept up."
Omar said he is optimistic about the short-term solution put forward by the Biden administration but added that in the long term, the answer could be "a partnership between private and public sectors" to share supply chain information to pinpoint the issue early on.
Karen Keating, president and CEO of the Small Business & Entrepreneurship Council, said the issues have been ongoing since the beginning of the pandemic. However, she said small businesses are trying to be proactive to stay competitive.
"Small businesses may have less sophisticated purchasing options, but they do have more flexibility due to their size," Keating said. She added that small businesses "communicate with customers and clients about the situation" and "stay in contact with their customers about possible disruptions and delays in their products and services" to keep up with current issues.
Kandace Loge, who owns Pidcock Glass, a four-employee business in Nelsonville, Ohio, said she has had trouble finding screen metal, an essential part of her work, since May, saying she's often had to wait several months before being delivered her orders.
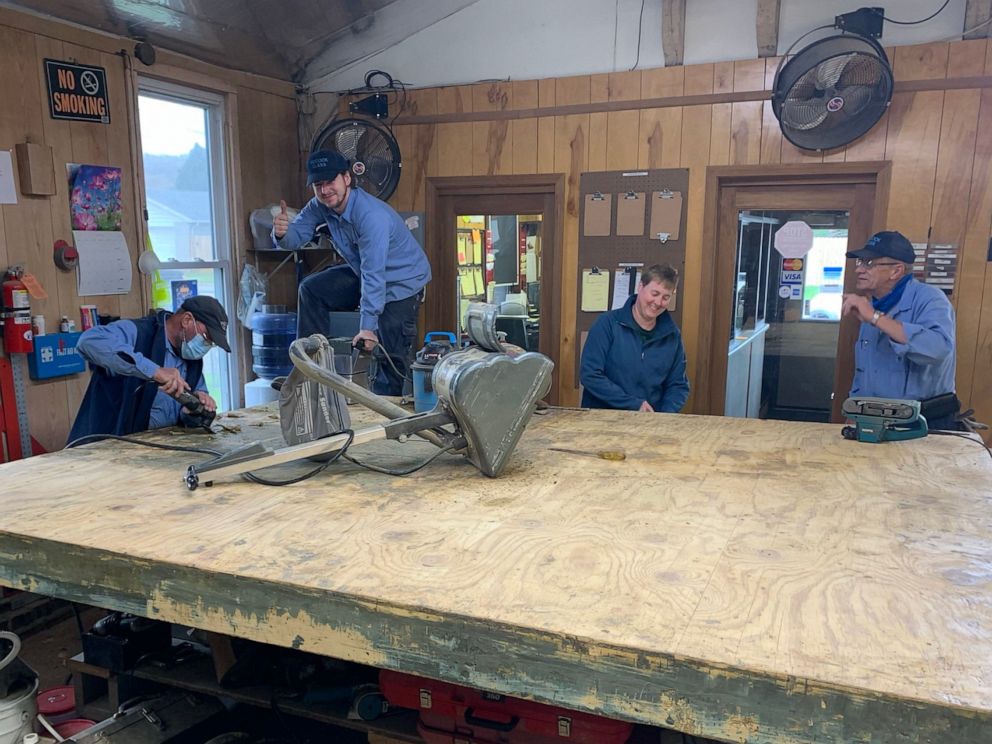
Loge, who has managed the company for almost 20 years, said her solution has been to be upfront with her customers.
"You have to be very honest with your customer; when they know that you are honest, they are usually very nice about it," said Loge.
Loge has changed her supplier, which has also meant a change in product sizes and changes to the company's usual workflow and equipment.
"I am now starting to adjust our budget and change the pricing on products," said Loge.
For many business owners, the concern remains the same: Will they be able to find the products they need, and will it affect their cost of production?
Plemons said he has the same thought every time he goes shopping for his business: "What am I not going to be able to find today?"