This Fortune 500 company has a plan for reopening amid COVID-19 -- and is sharing it with everyone
Lear Corp., a global supplier of vehicle components, is opening up its playbook.
There's no turn-key manual for restarting a business in the throes of a deadly global pandemic, ebbing in some parts of the world, surging in others, just as there aren't hard-and-fast rules for social distancing within a company commissary or on a factory floor when even the slightest oversight could cascade into catastrophe.
But one Fortune 500 company is aiming to help fill that void, using the downtime made necessary by the uncontrolled spread of the novel coronavirus to develop and publish a meticulously detailed handbook for reopening its manufacturing facilities while minimizing the potential risks in getting back to work, where and when permitted by law.
"I felt there wasn't anything off-the-shelf you can take and use," said Ray Scott, president and CEO of Lear Corp., an automotive parts supplier based in Southfield, Michigan, and which has 271 production plants in 39 countries, including in China's Hubei Province, where the novel coronavirus first was detected.
"We have incredible knowledge in Asia, and we have significant business in Italy, in Spain and all throughout Europe," Scott said in a phone interview with ABC News. "My mission was to take everything we have. We took the best practices of every single plant."
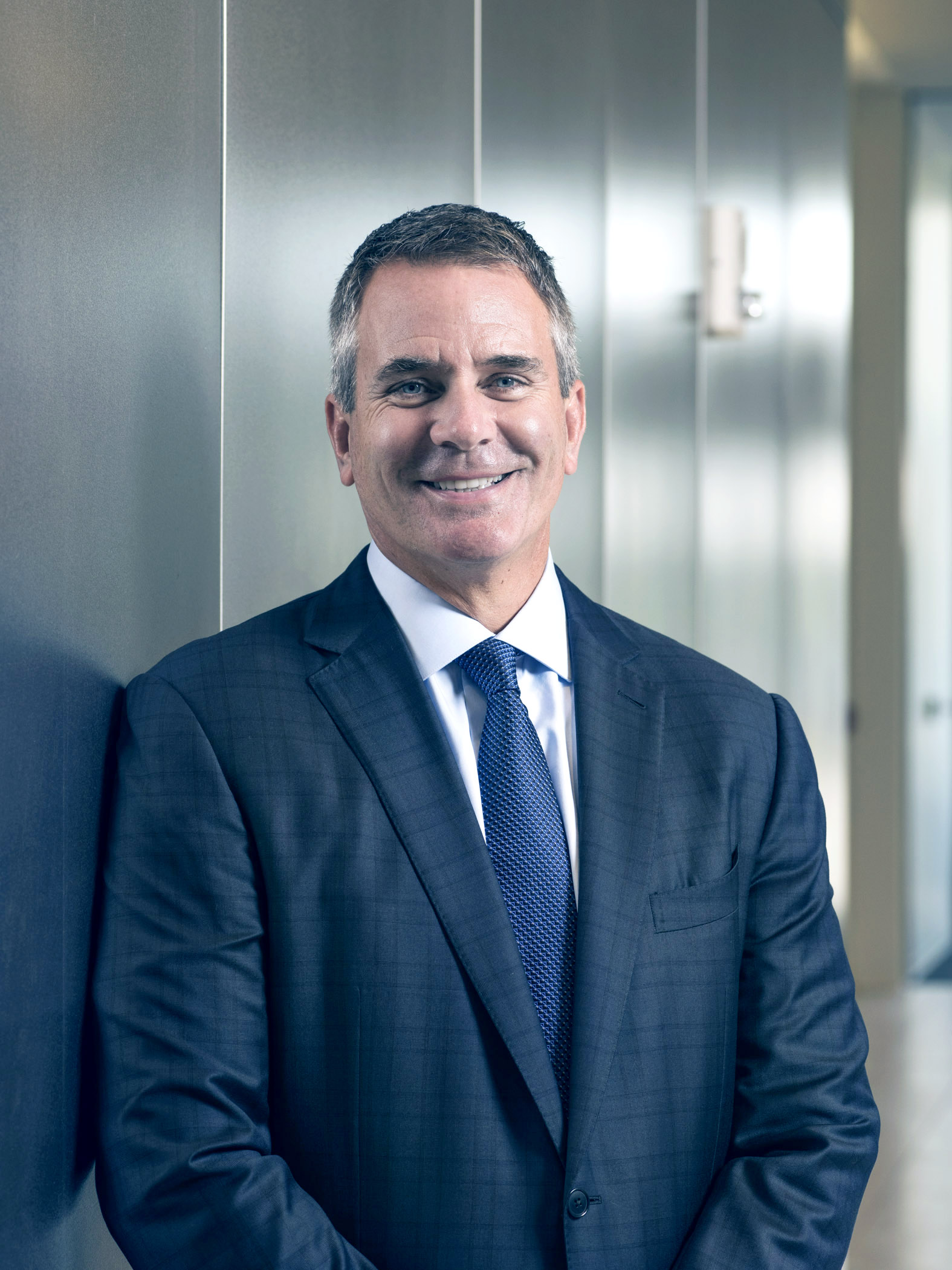
The Lear Corp. may not be a household name, but the 103-year-old maker of electrical components and seats for cars reported more than $21 billion in sales in 2018, placing the company No. 147 on Fortune's annual list.
Lear has 30 manufacturing facilities in the U.S., but like just about every other multinational manufacturing firm, the company's had to temporarily slow or idle production at many of its plants because of COVID-19.
Some of the company's plants were quickly reconfigured to make protective face masks -- both for employees and for local communities -- and Lear said it's now producing more than 125,000 daily. Many have been donated to medical providers and first responders near the company's Michigan headquarters.
Working from home under restrictive shelter-in-place orders, Scott said it became clear that things would need to dramatically change in the company's workplaces, at least until a vaccine is widely available. For some 170,000 Lear employees, returning to work will prove anything but business as usual.
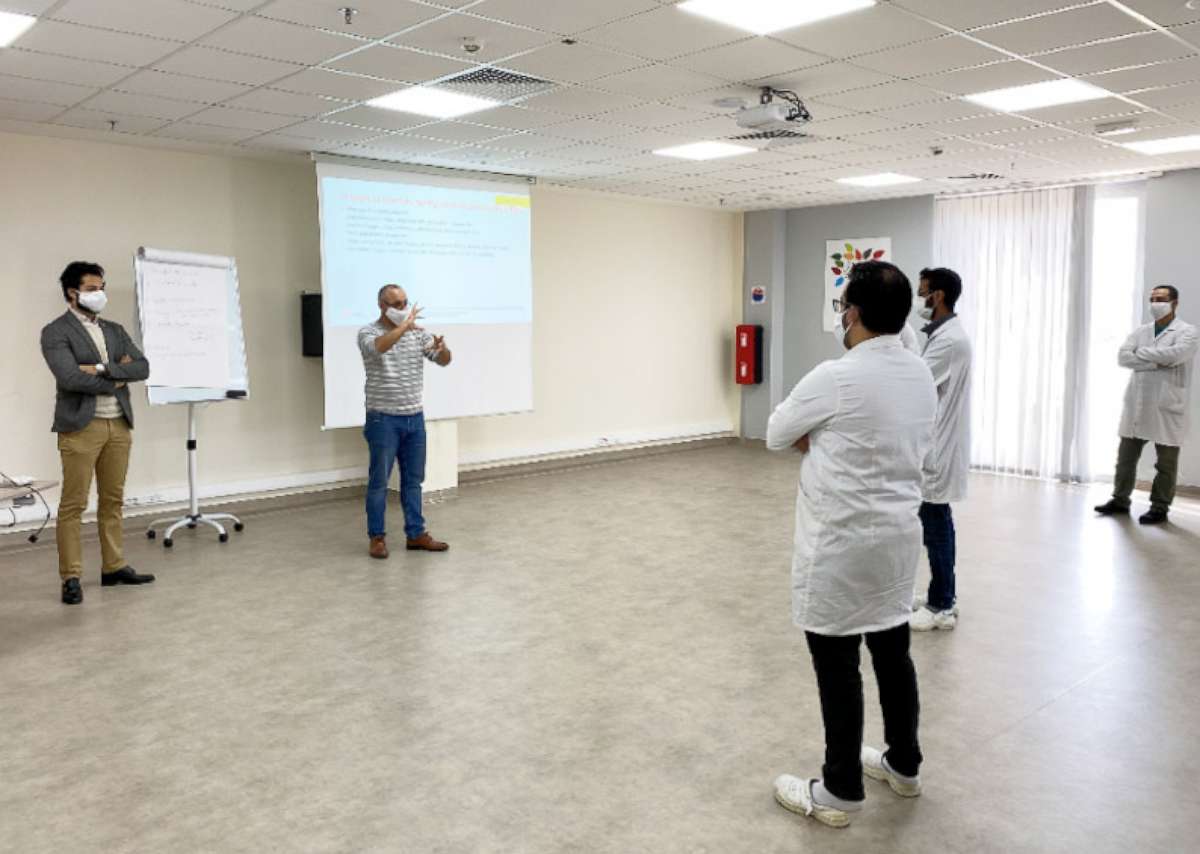
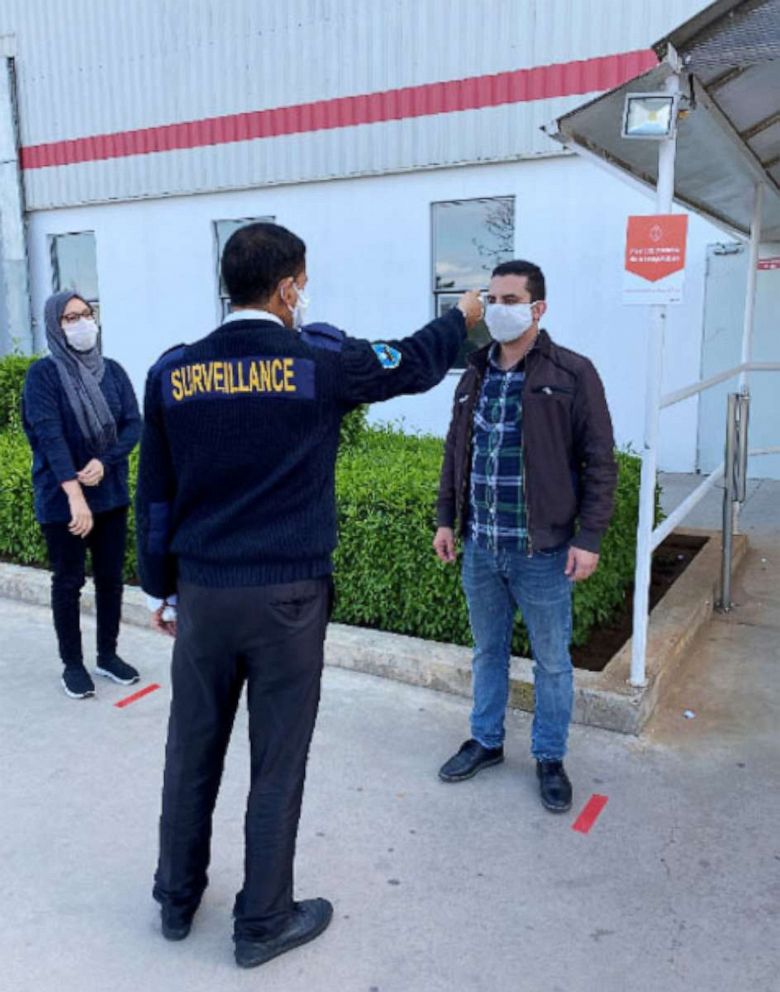
Scott brainstormed remotely with company leaders from human resources, information technology, health, safety, communications and operations to develop a best practices guide they're calling the "Safe Work Playbook: An interactive guide for COVID-19 Pandemic Preparedness and Response."
The manual, a 51-page, highly detailed set of protocols for facilities on everything from creating an in-house pandemic response team to sanitation procedures for production lines to social distancing in break rooms, seeks to meld company practices with guidelines issued by the World Health Organization and the U.S. Centers for Disease Control and Prevention.
The requirements, which will be updated frequently in line with evolving medical guidelines, are designed to be strictest in areas hardest hit by the virus.
"The manual is from A-Z how we run our business in our plants and in our offices around the world," Scott told ABC News. "The intent is to protect our employees to the best of our ability."
All employees will receive health screenings and contactless temperature checks when entering buildings at the start of their workdays, and start times of shifts will be staggered to promote social distancing. Security guards at entry points will help see through these guidelines, and employees will be tasked with monitoring doors and wiping down surfaces -- even on time clocks.
At lunch breaks, half of a crew could be asked to eat outside or in their cars so there's ample social distancing for employees who remain in the lunchroom. Chairs could be marked by signs reading "yes" or "no" to encourage workers to maintain distance among themselves.
A section of the manual that outlines sanitation procedures instructs that tools and control buttons in common work spaces on production lines should be cleaned at least three times per shift with a hospital-grade disinfectant. Forklifts should be sanitized after each use. Protocols also specify that each facility maintain at least a 30-day supply of disinfectants, masks and other personal protective equipment for employees and contractors responsible for cleaning.
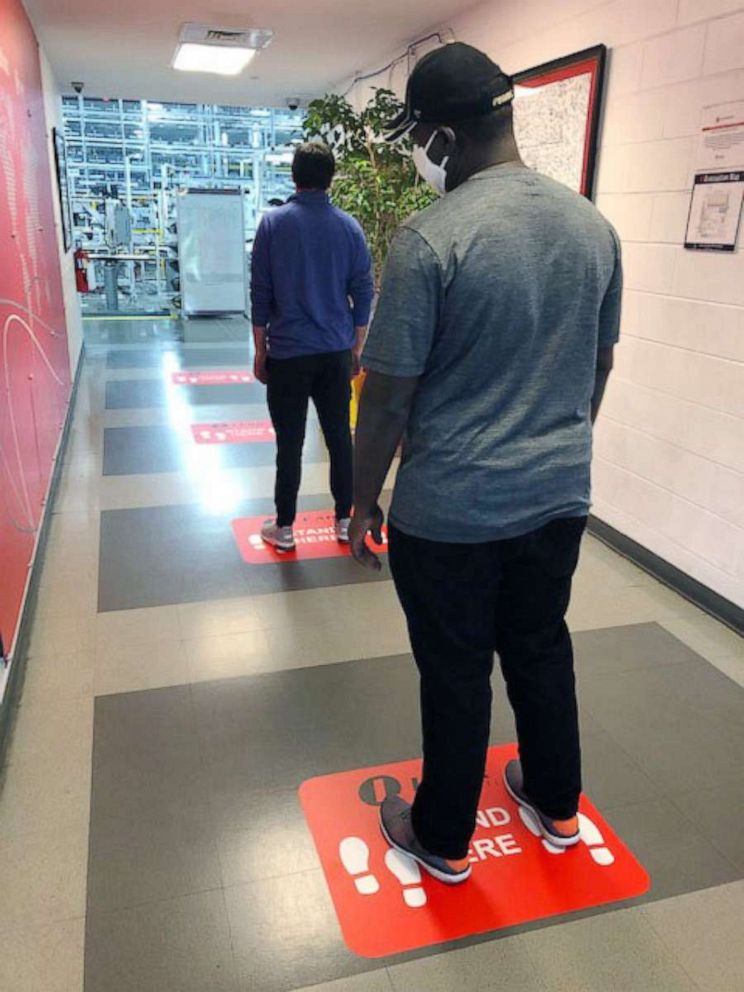
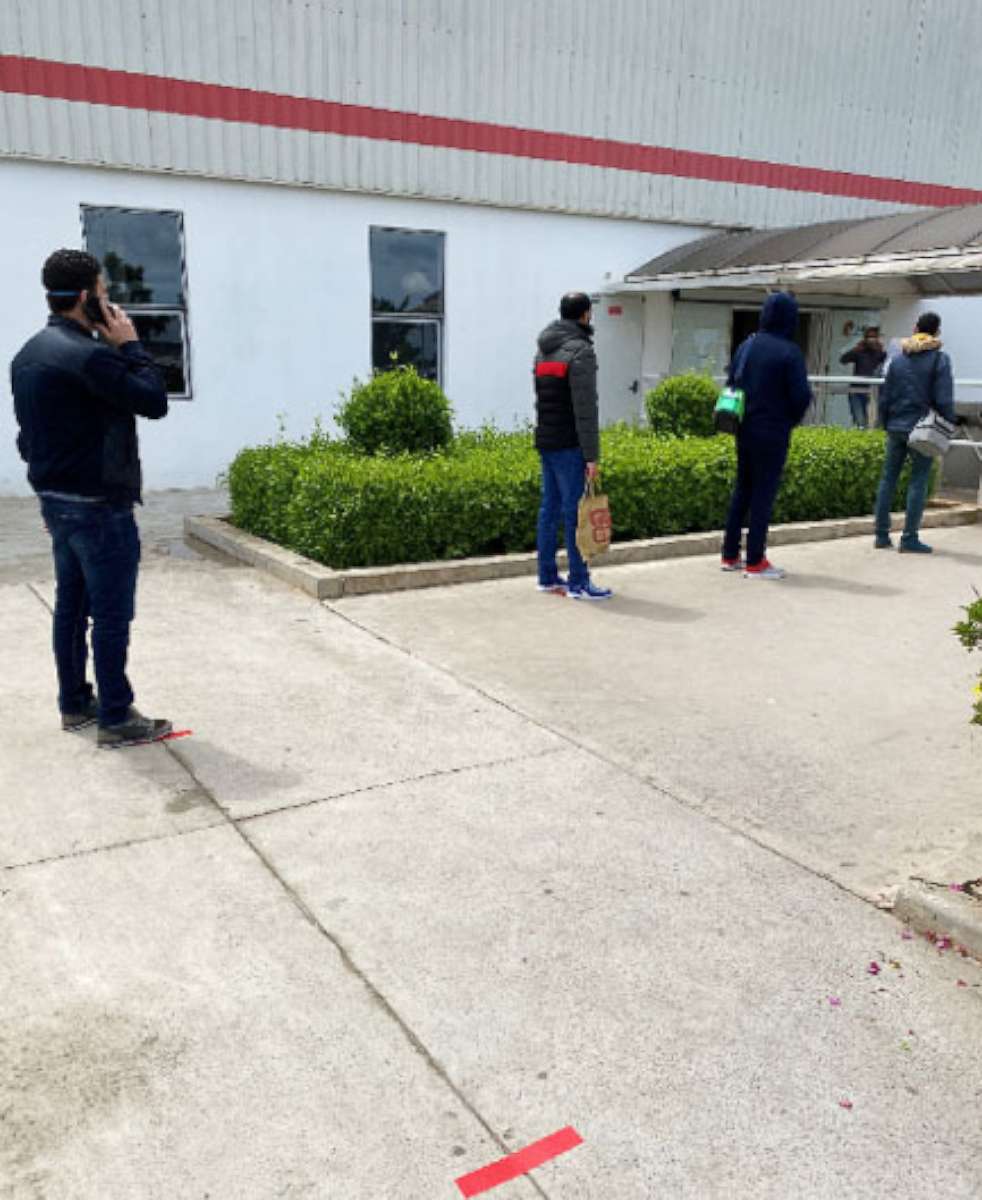
By adhering to its new playbook, Lear said, production capacity at facilities in China has recovered to about two-thirds of pre-COVID 19 levels. Meanwhile, U.S. employees in regions with fewer virus-related incidents are being actively trained to implement similar measures once local governments determine resuming operations is safe.
After completing the manual, leadership at Lear decided to post it on the company's website as downloadable digital content, Scott said, in the hope of benefitting other companies. After all, it won't do Lear much good to make components for cars if no one's building or buying cars.
"I thought in order for everyone to get up and running, we should share this widely," Scott added.
A Lear spokesman said that through Thursday the manual had been downloaded more than 12,000 times.
In a letter to fellow business leaders that now accompanies the manual, Scott wrote: "Re-establishing a workplace where employees feel comfortable performing their jobs safely is a multifaceted challenge. It is our hope that by sharing this resource we can help your organization accomplish the same goals, as everyone adapts to new operating protocols in today's still challenging conditions."